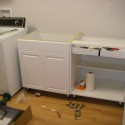
In the laundry room, I used some ready-to-assemble cabinets from Home Depot, and some off-the-shelf laminate counter top from Rona that I had them cut at the store.
The sink came with a template, so I traced that onto the countertop with a sharpie, use a hole saw on the edge to start it off, and then cut out the shape with a jigsaw.
Almost constantly, the box stores have different promotions going on (eg, I bought the cabinets during a 10% off all kitchen cabinets sale), and I’ve tried to take advantage of these as much as I can.